We are committed to cultivating a culture of operational discipline, leading to improved efficiency, quality, and risk management.
Refinery workers in Tuscaloosa, Alabama
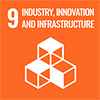
Our Operational Management System (OMS) incorporates processes and procedures that promote operational excellence. The OMS applies to company activities from facility design, construction, operations through to decommissioning, and throughout the entire lifecycle of the business. The OMS offers an integrated approach and the flexibility to address a wide range of risks, impacts or threats related to operational efficiency, occupational health, and safety; environmental and social responsibility; process safety, quality, and security.
Operational Management System
Given the breadth and depth of our operations, it is critical that we have consistent processes across our various business units, projects, and teams operating worldwide.
Hunt’s Operational Management System provides a consistent framework for assessing, managing, and optimizing processes and performance. It ensures we have the procedures and controls in place to operate and grow as an organization in a deliberate and sustainable manner.
The elements of the Operational Management System are aligned into a logically sequenced framework that can guide work at any level of the organization. Each standard within the framework is supported by processes that Hunt expects all employees to meet.
Hunt management systems are aligned with and in some cases certified by International Organization for Standardization (ISO).
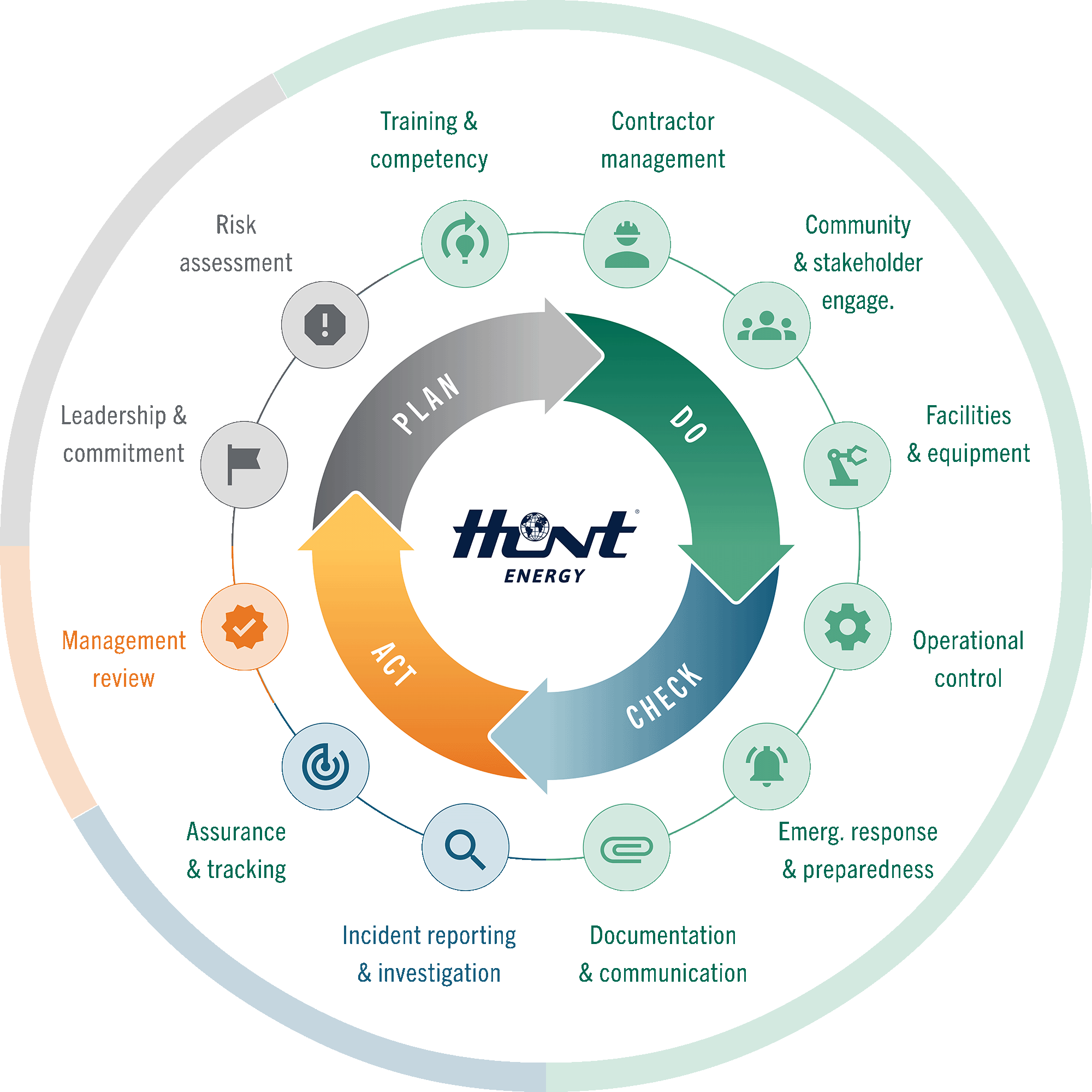
- Leaders establish policy, provide perspective, and demonstrate commitment
- Processes are well established and communicated to all employees
- Clear expectations are set and provide the support and resources to drive implementation
- Performance is tracked and analyzed against our goals and objectives
- Risk is managed by identifying hazards, assessing severity and probability of occurrence
- Control measures are developed and implemented to remove or reduce the level of risk
- Risk assessments are conducted for new and existing projects on an ongoing basis
- When changes to an operation occur, risk assessments are reviewed and updated
- Our employee’s knowledge, skillset and qualifications are vital to managing risk
- We ensure skilled and competent workers through training and development opportunities
- Initial and ongoing training is conducted to ensure competency and continuous growth
- Employees participate in hands on training, classroom, and web-based learning
- Contractors are screened and selected using processes that assess their ability to perform work safely and efficiently
- Performance requirements for contractors are established and reviewed
- Contractor performance is tracked with frequent and continuous feedback provided to ensure open communication and continuous improvement
- We actively engage with our interested community and stakeholder members to maintain open communication, trust, and quickly address any concerns
- Hunt partners with local community, state, and federal industry groups to help inform regulators and governmental decision makers about our operations
- We meet regularly with local and state emergency responders to ensure they are aware of our operations and to develop relationships with our employees
- Our facilities are designed, constructed, commissioned, and maintained to ensure a safe and efficient workplace
- Equipment selection and procurement processes ensure we meet proper specifications
- Operations, maintenance, and emergency procedures are documented and well communicated
- Pre-Start Up Safety Reviews are conducted to ensure facilities are safe to operate
- Changes to equipment or procedures are managed by a Management of Change (MOC) process
- Operational controls are our core procedures that prevent or mitigate risks and incidents, and ensure consistency across the company
- Operational control procedures have been established to ensure employees’ actions are aligned with company and industry best practices
- Controls include equipment, engineered safeguards, project designs, personal protective equipment, and administrative procedures
- Specific control procedures are developed for high risk activities
- Emergency Response Plans exist to identify processes, equipment, personnel, and resources necessary to respond to emergencies to protect our people, the environment, and the public
- A universal Incident Command Structure is applied to all emergencies
- Training and drills are conducted periodically with employees and third party response personnel which include classroom and field based exercises
- Processes have been established to ensure easy approval, storage, and retrieval of company documentation
- Effective transfer of information across all levels of the organization is critical for our success
- Information related to state, federal and country regulations is kept updated and available
- Internal guidelines, procedures, permits, and work instructions are well organized and readily accessible
- Processes are in place for quick communication of important and time sensitive information
- All incidents are reported and investigated, regardless of severity
- Incidents and near misses are investigated timely to determine root cause, identify corrective actions, and prevent reoccurrence
- High Potential Incidents (HIPOs) are distributed across the organization to share lessons learned
- Incident trends are analyzed and reviewed frequently to identify opportunities for improvement
- Incident investigation results are assessed periodically by our HSE Management Committee
- Operations are inspected and audited by multidisciplinary teams at scheduled frequencies to ensure compliance with established requirements
- Measuring and monitoring data are essential tools for tracking operational performance, assuring that objectives and targets are met and identifying opportunities for improvement
- Findings from inspections and audits are well documented and tracked to closure
- By regularly assessing operational performance, management adjusts programs and resources to generate the best results
- The ongoing review of our procedures and processes helps to ensure continuing suitability, adequacy, and effectiveness of the system
- Periodic reviews ensure the employees and system remain accountable and present the opportunity for discussion between employees and management to find areas for improvement
- Performance is evaluated against our goals and objectives to ensure all expectations are met